Aeroacoustics Research Could Help Quiet Upcoming Supersonic Business Jets
Groundbreaking aeroacoustics research being done for the Federal Aviation Administration (FAA) by researchers at the Georgia Institute of Technology (Georgia Tech) and Savannah-based Gulfstream Aerospace could lead to quieter operation of future supersonic civilian aircraft, including business jets.
Such aircraft could dramatically reduce flight time for passengers and crew, but because their engines can’t take advantage of certain sound-reducing technology now used in subsonic aircraft like commercial airliners, additional technology will be needed to mitigate noise. Research being done in unique aeroacoustics test facilities at the Georgia Tech Research Institute (GTRI) will provide detailed data to be used in computer models designed to help optimize engine configurations for the supersonic aircraft.
Groundbreaking research being done for the Federal Aviation Administration by researchers at Georgia Tech and Savannah-based Gulfstream Aerospace could lead to quieter operation of future supersonic civilian aircraft, including business jets.
While research at NASA and other organizations focuses on countering sonic booms during supersonic flight, the FAA project – funded at Georgia Tech through the Center of Excellence for Alternative Jet Fuels and Environment (ASCENT) – is addressing engine sound generated when the aircraft will be flying at subsonic speeds as they take off and land. Key to controlling that noise may be the configuration of engine structures that mix heated air exiting the engines with cool air flowing around them. Designing the mixer is a multidisciplinary task that must carefully balance engine performance against noise to meet aircraft-level requirements.
“Ultimately, the goal will be to design noise suppression for the engines,” said the principal investigator of the project Krish Ahuja, regents professor in Georgia Tech’s School of Aerospace Engineering and regents researcher at GTRI. “But data about the effects of different nozzles is just not available to support the computational modeling necessary to guide the design of optimal mixers. Modeling will depend on issues such as velocity profiles and turbulence intensity that must be based on real data that we are acquiring.”
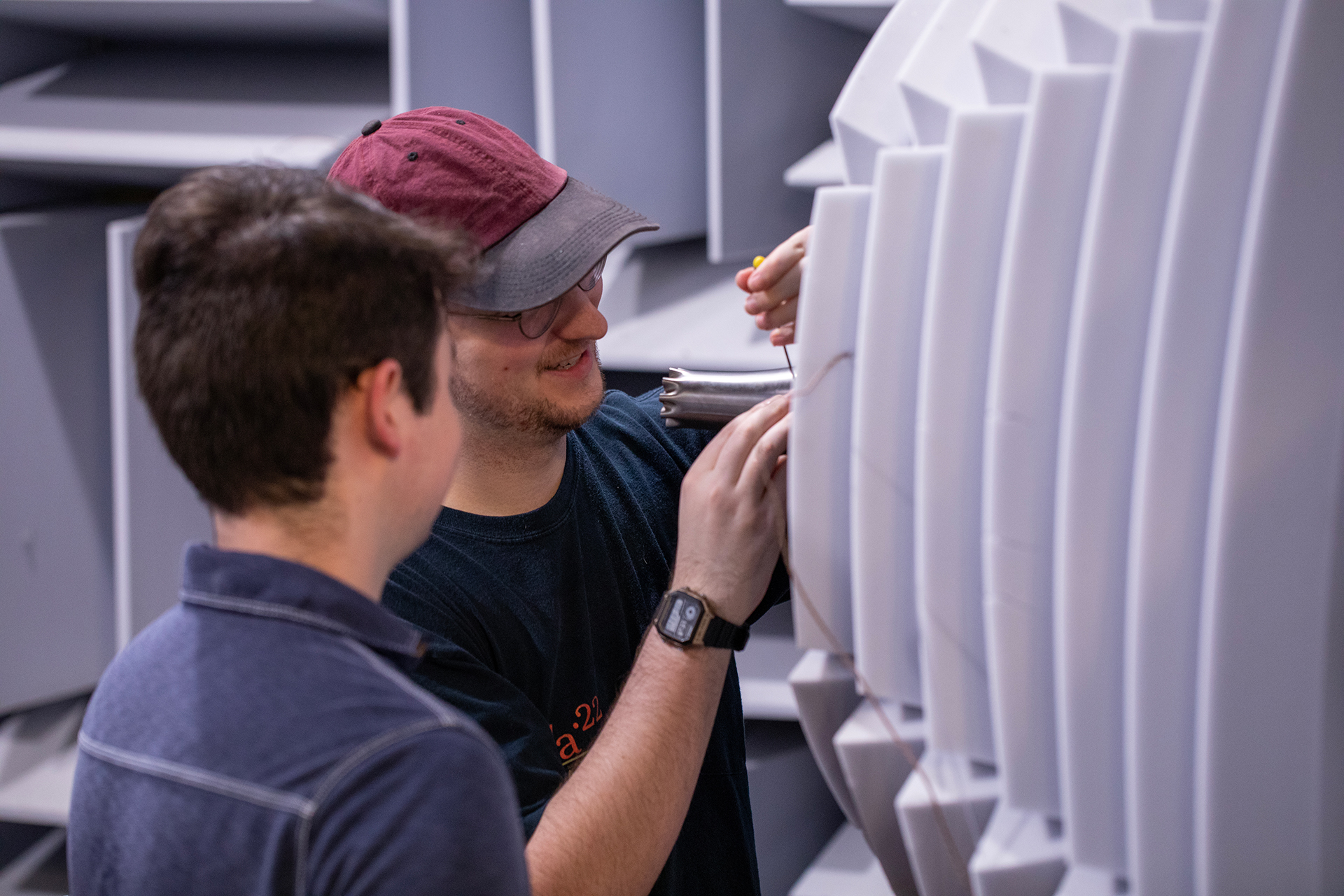
Georgia Tech graduate student Jackson Larisch and recent graduate Reagan Mayo install a test nozzle in GTRI’s Anechoic Static Jet facility, where banks of microphones record sound from the nozzle as air passes through it, while other instruments measure air flow velocity and pressure. (Credit: Sean McNeil, GTRI)
The data is being gathered from equipment in GTRI’s Anechoic Static Jet facility, which pushes high-speed air through nozzle and mixer configurations under test, while banks of microphones record the sound at different frequencies and instruments measure such factors as velocity, pressure, and turbulence. The system also pinpoints where the sounds originate.
In addition, another set of instruments in GTRI’s Flow Diagnostic Facility visualizes the high-speed air passing through the nozzles using technology known as schlieren imaging. This visualization is done at very high speeds to provide understanding of the movement of plume turbulence responsible for jet noise.
The data gathered at the two facilities will be provided to computational modeling teams at Stanford University, Penn State University, and the University of Illinois, who will use it to validate their multi-fidelity noise prediction models and make the conclusions available to the FAA – and companies interested in developing civilian supersonic aircraft.
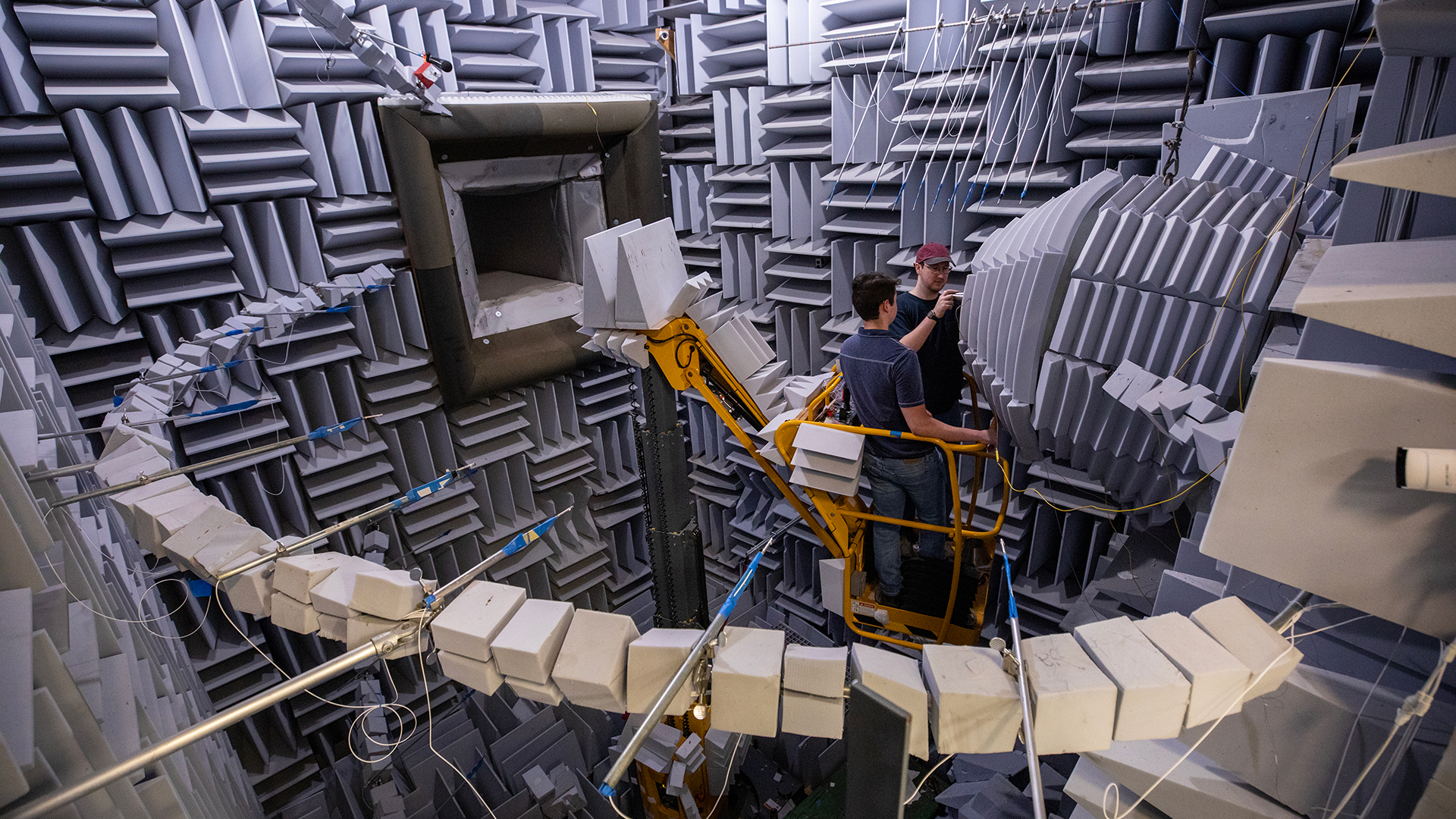
Georgia Tech graduate student Jackson Larisch and recent graduate Reagan Mayo install a test nozzle in GTRI’s Anechoic Static Jet facility, where banks of microphones record sound from the nozzle as air passes through it, while other instruments measure air flow velocity and pressure. (Credit: Sean McNeil, GTRI)
In earlier project stages, engine plans, baseline nozzle information and testing designs were developed by Georgia Tech’s Aerospace Systems Design Laboratory, which is headed by Regents Professor Dimitri Mavris. The design work focused on engines that would be needed for a 55-passenger supersonic aircraft.
A designer and manufacturer of business jets, Gulfstream has been studying the design space for supersonic aircraft for nearly 30 years, and expects the research – both the data-gathering and computational modeling that follows – will help advance the aviation industry’s development and production of civilian supersonic aircraft.
“The interdependencies between noise, emissions, and performance in supersonic aircraft are more complex than in subsonic aircraft, so reducing design uncertainties is essential to risk reduction and balancing design objectives,” said Joseph Gavin, staff scientist at Gulfstream who is working with the Georgia Tech researchers. “An intermediate step of this work is to provide the aviation industry with better tools to solve the competing design objectives of supersonic aircraft, but the ultimate goal is to mitigate landing and takeoff noise of future supersonic aircraft around our communities.”

Nozzle incorporating a lobed configuration is tested in GTRI’s Anechoic Static Jet facility. Designed and fabricated by Gulfstream for the research program, the suppressor nozzle would help mix hot exhaust from the engines with cooler air circulating around them to help control noise. (Credit: Sean McNeil, GTRI)
The data gathering is being supported by Gulfstream as part of the project’s cost-sharing agreement with the FAA. The company is providing its industry perspective and expertise to help guide the researchers and has provided outside review of the experimental work. Gulfstream is also designing and fabricating the non-proprietary jet exhaust test articles being used in the GTRI experimental flow and acoustic measurements.
So far, two nozzles incorporating a lobed configuration have been designed and fabricated for preliminary evaluation. Contained within a co-flowing stream, commonly referred to as the bypass stream, the lobed nozzles would help mix hot exhaust from the engines with cooler air circulating around them to help control noise. The configurations are being tested by a team of researchers and graduate students led by GTRI Research Engineer Nick Breen.
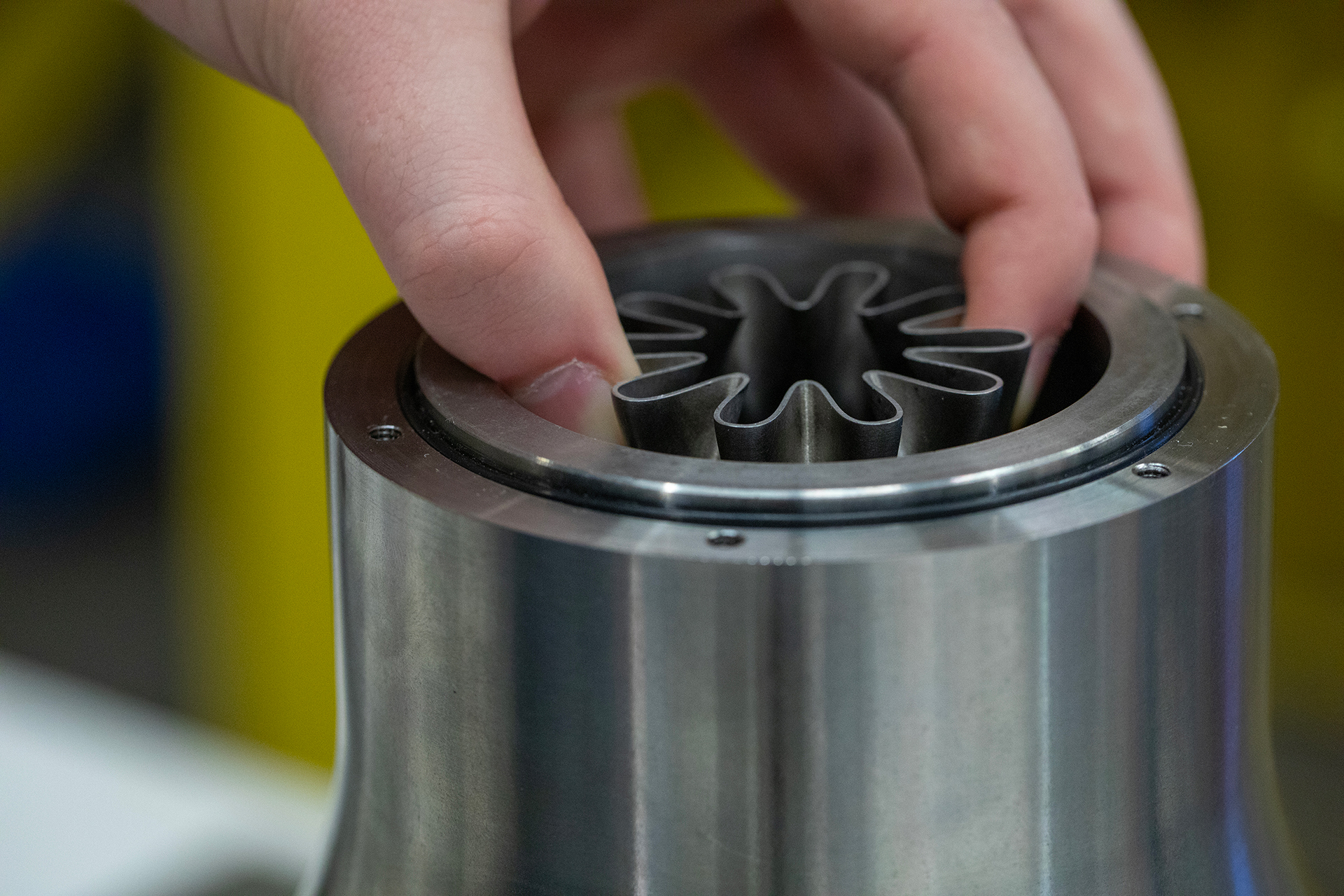
Image shows how a lobed suppressor nozzle would operate within the bypass stream exiting a jet engine, which is one of the configurations of the research setup designed to study mixed airflow. (Credit: Sean McNeil, GTRI)
The computational models that will ultimately come out of the work will help designers of the supersonic civilian aircraft make important decisions about tradeoffs between engine noise, weight, and thrust. Engine thrust affects factors such as fuel consumption and aircraft performance, yet noise produced by the aircraft will affect their acceptance by communities near the airports where they will operate.
“The tradeoffs between noise and thrust will be important to manufacturers and aircraft operators,” Ahuja noted. “Because the aircraft will operate at supersonic speeds, the form factor of the engines will affect issues such as drag and weight.”
Subsonic passenger aircraft have mitigated noise in large part by using high bypass turbofan engines which use a large ducted fan at the front of the engines to force air toward the rear of the engines. By increasing the mass of air moved, these engines operate at lower velocities that reduce noise and are more energy efficient. But these engines would not be feasible for supersonic flight.
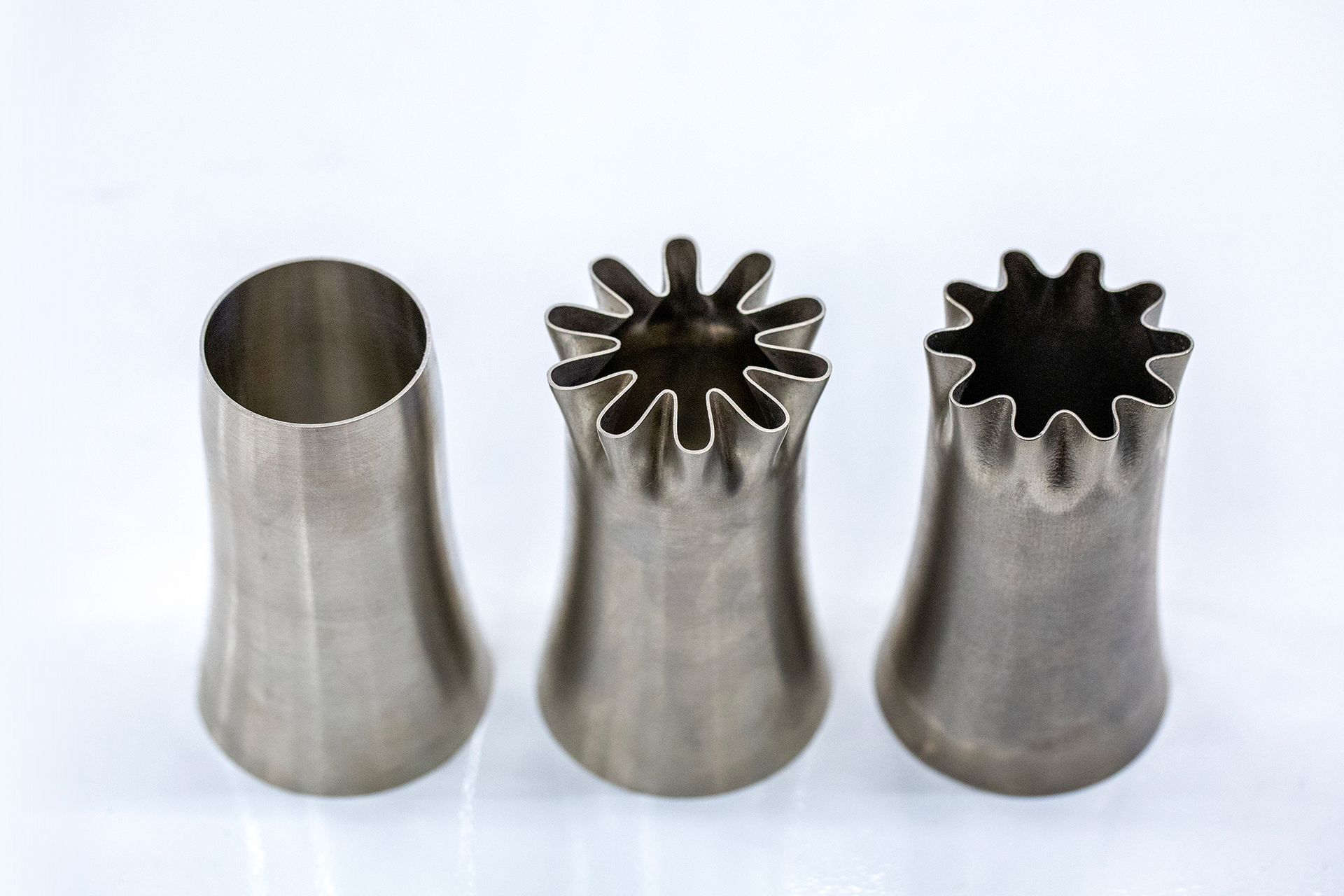
Non-proprietary jet exhaust test articles designed and fabricated by Gulfstream for aeroacoustics testing. (Credit: Sean McNeil, GTRI)
The data provided by the experimental research will enable development of low-, medium- and high-fidelity jet noise prediction methods that developers of the supersonic aircraft can use to help make design decisions.
“One of the key challenges of designing a supersonic aircraft is maintaining the functionality of a subsonic aircraft and preserving noise and emissions performance all while flying faster than the speed of sound,” noted Gulfstream’s Gavin. “With the data and tools that will come from this ASCENT project, the research team is advancing the industry another step closer to environmentally responsible supersonic flight.”
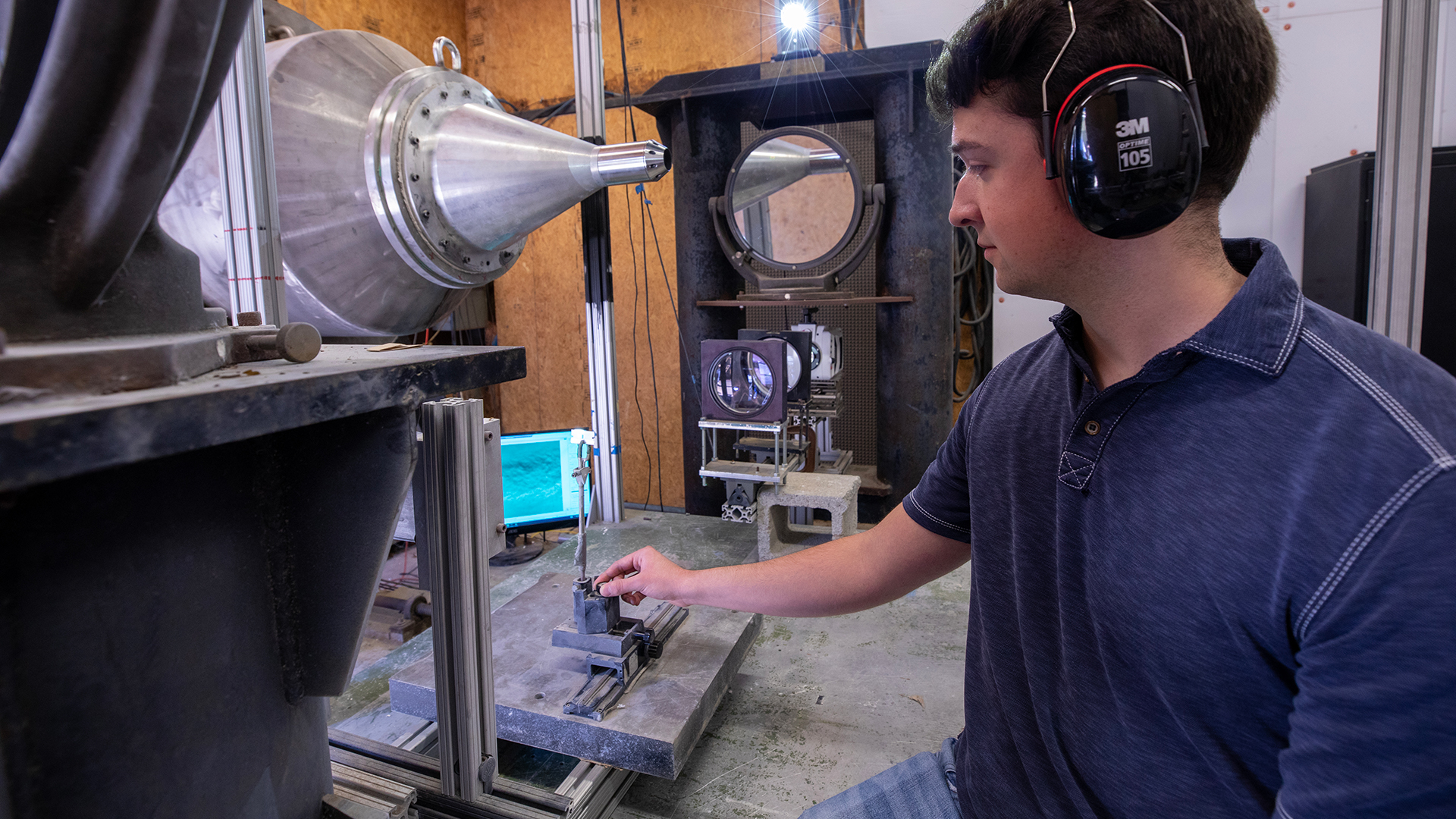
Researcher Regan Mayo, a recent Georgia Tech graduate, adjusts equipment in GTRI’s Flow Diagnostic Facility to visualize the high-speed air passing through the nozzles using technology known as schlieren imaging. (Credit: Sean McNeil, GTRI)
Writer: John Toon (john.toon@gtri.gatech.edu)
GTRI Communications
Georgia Tech Research Institute
Atlanta, Georgia USA
The Georgia Tech Research Institute (GTRI) is the nonprofit, applied research division of the Georgia Institute of Technology (Georgia Tech). Founded in 1934 as the Engineering Experiment Station, GTRI has grown to more than 2,900 employees, supporting eight laboratories in over 20 locations around the country and performing more than $940 million of problem-solving research annually for government and industry. GTRI's renowned researchers combine science, engineering, economics, policy, and technical expertise to solve complex problems for the U.S. federal government, state, and industry.